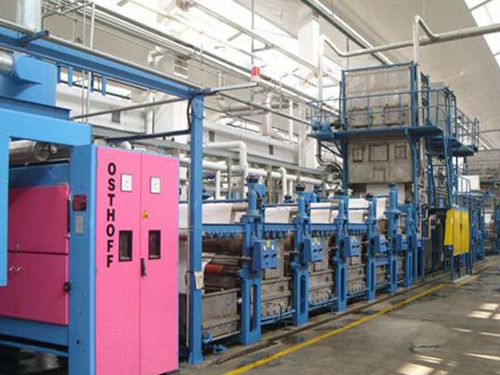
The textile printing and dyeing industry is a high-energy-consuming, highly polluting, labor-intensive industry. According to statistics, China's textile sewage discharge accounts for the third largest amount of sewage discharged in the country, and the largest amount of emissions comes from textile printing and dyeing. In recent years, China’s labor costs have been rising at an average annual rate of 10%, and there are many production processes that require a lot of labor in the printing and dyeing process of textile products. By responding to the loss of the demographic dividend of our country through the intelligentization of equipment, the promotion of green environmental protection in the production process is a top priority for the development of printing and dyeing equipment.
Stand-alone smarter
Recently, Jiangsu SEG Textile Machinery Co., Ltd. held a new product promotion conference. At the meeting, the company launched a new intelligent environmental protection high-speed decoction bleaching combined machine. According to reports, the equipment was digested and absorbed by Jiangsu SEG Corporation and advanced European design concept, and it was transformed and innovated after production. It will soon be exported to the Turkish market. Bao Dequan, general manager of SEG, told reporters that this model represents the highest level of printing and dyeing machinery and equipment manufacturing in the world today, and its key components are in line with international standards. The equipment has outstanding performance in high speed, high efficiency, energy saving and environmental protection.
Bao Dequan said that at present, the intelligent development of single printing and dyeing equipment in China is very good. Apart from the well-known role of replacing labor and saving labor, smart equipment has another important advantage in its control over production costs and production management. In terms of cost, automatic feeding is achieved through intelligent equipment, which allows precise control of water, electricity, and steam consumption and reduces unnecessary waste. In terms of management, the intelligent system realizes online monitoring and remote diagnosis through ERP, Internet, local area network, etc., which is more conducive to order management and process storage. In particular, in the process of customer's re-production, the device's stored prescriptions are effectively avoided. The color difference between the printing and dyeing effects.
Hangzhou Open Source Computer Technology Co., Ltd. has also developed a number of intelligent products. According to Xu Changyuan, manager of Hangzhou Open Source Marketing Department, the company's intelligent products mainly consist of three major blocks, namely, various types of screen making machines, automatic computerized pulping systems, and MES printing and dyeing online collection systems. Among them, the company's open-source Blu-Ray system uses a precise focusing, stable UV laser system to directly expose patterns on printing blanks pre-coated with sensitized adhesive to obtain the required nets for printing, overcoming the traditional medium-making process for media. Dependence, to achieve low-cost, high-speed, high-precision direct network. The open-source Blu-ray machine can complement each other with open-source other network products to meet the differentiated production needs of customers in high schools and low-end industries, and create the best network production benefits for customers.
Automatic computerized liquid mixing system applies color space theory, paradigmatic reasoning, color light-viscosity mathematical model, database, full-closed loop control and precision weighing technology, etc., to printing and pulping, dyeing and dosing, and can accurately control the key process of pulping. Parameters to achieve fast automatic slurry mixing and residual slurry reuse to achieve energy conservation and emission reduction.
Changzhou Hongda Technology Group has done a good job in the research and development of the intelligent online monitoring system for printing and dyeing equipment. Gu Ren, chairman of the group, said that Changzhou Hongda's online monitoring system mainly consists of three categories: environmental digital systems for printing and dyeing, digital energy-saving and emission-reduction systems, and intelligent information management systems for printing and dyeing production. Printing and dyeing environmental protection digital system products include digital monitoring platform for sewage treatment, on-line detection of smoke emission from stereotyped machines, etc.; digital energy-saving and emission-reduction systems include intelligent steam energy-saving systems, WT series precise water consumption online measurement and control systems, etc.; printing and dyeing production intelligent information management and control systems have HVMC-15 series intelligent full-width weaving machine, batik rotary screen machine visual automatic flower system, HV-TT20 intelligent fabric density meter, HD-100 hydrogen peroxide concentration online detection control system and PH-500 PH value online detection and control System and so on. The successful development of these systems has basically achieved full monitoring of the printing and dyeing production process.
Continuous effectiveness doubled
Talking about the current status of domestic printing and dyeing equipment intelligence, Li Yi, vice president of the China Textile Machinery Association, believes that the intelligence of printing and dyeing equipment is mainly reflected in information flow and logistics. At present, various on-line monitoring systems developed by domestic textile machinery companies are relatively mature, and they have achieved the collection and processing of various information in the production process. In terms of logistics, the company's R&D products have basically achieved the intelligence of stand-alone machines, but have been different in production. Between the processes to truly realize the entire process of continuous intelligentization, currently only Shandong Kangpinna Group has developed the “counter-sleeve digital automatic dyeing technology and equipment packageâ€.
At the National Science and Technology Awards Conference recently held, the “Complete Dyeing Technology and Equipment for Digital Yarn Yarn of Cheese Yarn†of Shandong Kangpinna Group won the first prize for scientific and technological progress. The results have overcome 10 key technologies such as automatic weighing, humidity control, and dyeing, which are of great significance in promoting the transformation and upgrading of the textile industry. According to reports, the system has been transformed from manual mechanization to single automation and then to automation systems. It has achieved innovation in the three major systems, especially in reducing labor, improving product quality, and saving energy and reducing emissions.
According to Liu Lin, general manager of Shandong Kangpinna Group, cheese dyeing is the key link for producing high-grade fabrics and improving product features and added value. For the current textile printing and dyeing industry, there are labor shortages, low production efficiency, poor stability of dyeing quality, and high energy consumption and waste water discharge. These problems affect the sustainable development of the industry. The equipment was developed through three major innovations: dyeing process, equipment and system. It is suitable for the digital automatic dyeing technology of cheese yarn, digital automatic dyeing equipment and the central automatic control system for dyeing production. It has created a digital automatic dyeing production line for cheese yarn and established a digital dyeing workshop to make China the first breakthrough in the world. The whole process of automated dyeing technology and the realization of engineering applications in countries.
This set of equipment can be used for the dyeing of cotton yarns, wool yarns, cotton yarns and other cheese yarns, and can also be expanded to the fields of dyeing and printing of grey fabrics. It can realize water saving of 27% for ton yarns, save steam 19.4%, save electricity 12.5%, and reduce sewage 26.7% of emissions. In China, 10 million tons of dyeing yarn will be dyed annually. After the promotion of this equipment, 300 million tons of water will be saved each year, 2.33 million tons of standard coal will be saved, and 297 million tons of sewage will be reduced, which will help promote the printing and dyeing industry to achieve high quality and high efficiency dyeing. The transformation and upgrading will be intensive. , large-scale production and low-cost, low-emission green industry.
The whole process of intelligence is the direction
With the rapid development of electrical automation technology, the complicated mechanical structures in printing and dyeing machinery and equipment have gradually been replaced by electrical control systems. The mechanical structure is greatly simplified, the failure rate is effectively reduced, the control accuracy is improved, and a qualitative leap in printing and dyeing machinery products is realized. . Li Yi believes that the results of single machine and on-line monitoring of domestic printing and dyeing intelligent equipment should be referred to as “digital controlâ€, and like “King yarn digital automatic dyeing complete sets of technology and equipment,†such as Conpinna realized. From the manual mechanization, the collection of stand-alone automation, to the full-process digitalization, and the leap of system automation, it is the true sense of intelligence, and it is also the future direction of intelligent equipment development.
In this regard, Bao Dequan also holds the same view. He believes that, combined with the development of printing and dyeing industry, the future development trend of printing and dyeing machinery and equipment in addition to simplifying the structure of the whole machine, to promote high-speed, high efficiency, to achieve the key process parameters of online monitoring, remote diagnostic technology, closely follow the textile personalized, functional In addition to the trend of development and the development of printing and dyeing equipment that can adapt to small batches, varieties, and machines, the more significant direction is to develop process equipment that can be used for continuous dyeing and finishing of knitted fabrics to improve the dyeing and finishing of knitted fabrics. Production efficiency, continuous process,
Peach Skin Fabric,Peachskin Jersey,Peach Skin Velvet,Polyester Peach Skin
SHAOXING SHUKE IMPORT AND EXPORT CO.,LTD , https://www.shuketex.com